Driven by the dual goals of carbon peaking and carbon neutrality, as well as the circular economy, the plastic recycling industry is facing unprecedented development opportunities. As the first critical step in plastic recycling production lines, the performance and efficiency of plastic crushers directly determine the quality and cost of subsequent sorting, washing, and pelletizing processes. In recent years, new technologies like artificial intelligence, the Internet of Things, and energy-saving transmission have been used more. Because of this, plastic shredders are changing quickly. They are moving away from old mechanical designs. Instead, they are becoming smarter, more all-in-one, and more environmentally friendly. This article will delve into the technological evolution, innovative applications, and future trends of plastic shredders, revealing the secrets and value behind this intelligent transformation.
I. Technological Evolution: From Traditional Mechanics to Intelligent Control
The development of the plastic crusher is a history of technological innovation intertwined with environmental protection demands. As early as the start of the 20th century, inventors had already created plastic shredders. At first, people mainly used them to process simple plastic items like bottles and bags. But later, plastic products became used everywhere, and the amount of plastic waste grew a lot. Because of this, the old shredding machines could not keep up with the need for fast and exact recycling.
1. The Principles Under Which Traditional Plastic Shredding Machinery Works
The early machinery for shredding plastics adopted the method of cutting the material with flat blades and then crushing it with an impact. The machinery or equipment comprised rollers that were rotated at high speeds by powerful motors so that the plastic product could be cut into pieces. This machinery had a simple design structure and was cheap to manufacture. It had some major drawbacks as well: high energy consumption, noisy operations, quick blade erosion, and the cut plastic particles were of uneven sizes. With the requirements of the highly efficient, accurate, and low energy consumption modern plastic recycling industry, the old equipment cannot meet those requirements.
2. The Evolution from Traditional Mechanical to Intelligent Equipment
Since the 21st century, with advancements in materials science, control technology, and sensor technology, plastic crushers have gradually transitioned from “mechanical drive” to “intelligent control.” Modern industrial plastic crushers come in a variety of types and are typically designed using a modular approach, equipped with high-efficiency, energy-saving motors, intelligent control systems, automatic lubrication devices, and remote diagnostic modules. These improvements enable shredding equipment to operate at faster speeds and with greater stability, while also reducing maintenance costs and energy consumption.
3. The Application Prospects of AI and IoT Technology in Plastic Crushing
Currently, artificial intelligence (AI) and Internet of Things (IoT) technologies are accelerating their integration into plastic crushing equipment. For example, equipment can automatically identify the type of plastic being fed into the machine through image recognition and deep learning algorithms, and adjust the crushing parameters accordingly. Meanwhile, sensors can monitor the equipment’s operating status in real time, such as temperature, vibration, and current, enabling fault warning and predictive maintenance. Using these technologies makes the equipment smarter. It also gives strong help to the plastic recycling industry as it changes to using digital methods.
II. Innovative Design and Optimization of Plastic Crushers
During the trend of making things smarter, the people who design plastic shredders are doing more than just making them crush better. They also think that being highly efficient, using less energy, and being good for the environment are just as important goals. This requires professional plastic crusher manufacturers to conduct in-depth exploration and optimization in multiple dimensions, such as structure, materials, and transmission systems.
1. The Core of Design for High-Efficiency and Energy-Saving Plastic Shredder

Under the “dual carbon” background, energy saving and emission reduction have been put as the primary task in the plastic shredder design. The actual core surrounding the high-efficiency and energy-saving plastic crusher design philosophy is described as “precision shredding” and “maximizing energy utilization.”Conventional shredding routines lead to a high degree of wasted energy consumption and energy loss. Contemporary design, on the other hand, focuses on the optimization of the geometrical structure of the shredding chamber so that more even and efficient force distribution of material within the chamber is achieved to reduce unnecessary tumbling and friction of material in the shredding chamber. For instance, some of the new designs are in blades in “W” or “V” shapes, which have better cutting angles because centrifugal force is involved.
2. Application of Energy-saving Motors and High-efficiency Transmission Systems
Variable frequency drive (VFD) technology is now standard for energy-saving motors and high-efficiency transmission systems. With VFD, motor speed can be adjusted infinitely based on actual load. This effectively avoids the low efficiency problem of traditional motors when they operate under partial load.
High-efficiency motors rated at IE3 or IE4 are also used. Direct drive or high-precision gear transmission systems replace traditional belt drives. These changes maximize energy savings by reducing losses during transmission.
Many professional plastic shredder manufacturers are exploring the use of permanent magnet synchronous motors in large-scale industrial plastic crusher machines. This further improves electrical energy conversion efficiency.
III. Intelligent Control Systems: From Automation to Intelligence
1. Use of Automation Control Technology in a plastic crusher
As of the present, most plastic shredders have the installation of PLC control systems through which the realization of automatic operation, including startup and shutdown of the equipment, speed adjustment, and fault alarm, has become achievable. More advanced systems are added with touch screens that really add man-machine interfaces remotely, make the data more complete, and facilitate equipment operation and maintenance.
2. Method of Implementation of Intelligent Monitoring and Fault Warning Systems
Now most of the plastic shredders are installed with a system of PLC controls that can carry out automatic operation-which includes the startup and shutdown of the equipment, speed adjustment, and fault alarm. More advanced systems have touch screens, really adding man-machine interfaces, remotely-first making the data more complete-and facilitating equipment operation and maintenance better.
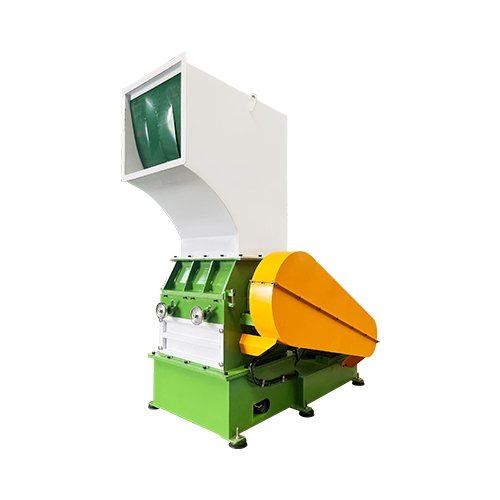
To monitor equipment operating status in real time, sensors for temperature, vibration, and current are usually installed at important points. The data that these sensors collect is pre-processed using edge computing and then sent to a cloud platform. Whenever the system detects that any of the observed parameters exceed the set threshold, conditions such as bearing temperatures exceeding set thresholds, the system automatically raises an alarm and stops the equipment to save the equipment from being damaged and to prevent safety incidents.
3. Advantages and Challenges of Intelligent Control Systems
Intelligent control systems can significantly improve equipment operational efficiency, reduce labor costs, and extend equipment lifespan. However, such systems also face challenges, including data security issues, compatibility issues between systems, and higher technical requirements for operators. In the future, people need to refine industry standards. They also need to strengthen technical training. They should promote the widespread use of intelligent control systems. These systems should keep getting better.
IV. Plastic Crusher: Supporting Sustainable Development
If plastic waste is directly introduced into the recycling process without prior processing, its large volume will lead to soaring transportation and storage costs, and it will be difficult to perform subsequent cleaning, sorting, and pelletizing. The shredding process can efficiently crush large plastic products (such as discarded water barrels, packaging films, and car bumpers) into uniformly sized fragments or particles. These shredded materials reduce the space they take up. This makes it easier to process them together. They also become standardized raw materials. These materials are ready for the next steps, like cleaning, drying, melting, and making pellets. This sets the stage for creating high-quality recycled plastic products.

Plastic crushers enable the recycling and reuse of plastic, significantly reducing the pressure on landfills and the environmental impact of incineration. Around the world, billions of tons of plastic waste are created every year. Most of this waste goes to landfills. Landfills use up valuable land. They also release harmful substances that pollute the soil and groundwater. Other plastic waste is burned. Burning creates toxic gases, like dioxins, and greenhouse gases. The recycled plastic industry is supported by industrial plastic shredders that reintroduce these otherwise discarded resources into the production cycle, directly reducing the amount of plastic entering landfills and incinerators.
The effective utilization and enhanced economic value of recycled resources are key contributions of plastic shredders to sustainable development. Through shredding and recycling, plastic waste that was once worthless or even required paid disposal is given new life and commercial value. For example, people can shred old PET bottles. Then they clean and process them. The result is recycled fibers. These fibers are used in clothes and carpets. Also, discarded PE and PP plastics can be recycled. They become things like trash bins, pipes, and pallets. This brings new ways for companies to make money. It also helps create a big industry. This industry involves recycling, sorting, shredding, and making new products. It creates many jobs. It also forms a green circular economic model. From this perspective, plastic crushers are not only environmental tools but also powerful drivers of the green economy.
V. Expanding Innovative Application Scenarios: From Single Shredding to System Integration
1. Application of Plastic Crushers in Medical Waste Treatment
Medical plastic waste, such as used intravenous infusion sets, syringes, and blood bags, poses a high infection risk due to direct contact with the human body or bodily fluids, and some materials may also be corrosive. Therefore, the processing of such waste has far stricter requirements than ordinary plastics, ensuring that no secondary pollution is caused during processing while effectively preventing the spread of pathogens. Specialized medical bottle crusher machines use many advanced technologies to keep things safe and protect the environment. These shredders have a very tight seal. This design stops dust, aerosols, or debris from getting out while shredding. It also helps keep away any possible biological dangers. By introducing a nitrogen protection system, an oxygen-deprived environment is created within the shredding chamber, which not only helps prevent oxidation or combustion of certain materials but also inhibits microbial activity, reducing the risk of infection. How is are plastic crusher innovatively applied in the medical industry?
2. Plastic Shredding Solutions for Electronic Waste Recycling
Electronic waste contains a large amount of plastic and metal mixtures, making traditional shredding methods inefficient for separation. The new generation of plastic crusher integrates metal detection, magnetic separation, and air separation functions to achieve efficient separation and recycling of plastic and metal. The core technology involves embedding a high-sensitivity metal detection system into the shredding process to identify metal impurities in real time and trigger sorting mechanisms. Subsequently, a strong magnetic separation device efficiently adsorbs iron-based metals, while an intelligent air separation module precisely sorts non-ferrous metals (such as copper and aluminum) and plastic fragments based on material density differences.
3. System Integration Solutions for the Recycling of Automotive Plastic Components
Automotive plastic components are diverse in type and complex in structure, making recycling challenging. Large amounts of old car parts are thrown away. These parts include things like bumpers and dashboards. They are made of mixed plastics and have complex shapes. Because of this, traditional shredders cannot process them well. Now, companies that make plastic crushers can help. They offer special shredders. These shredders turn slowly but have strong power. Sometimes, these companies also add extra shredders for early processing. These special shredders can handle tough, big plastic waste. They shred the waste efficiently. This makes it possible to recycle the materials afterward.
Ⅵ. Future Outlook for Plastic Shredder
Looking ahead, the plastic shredder will evolve toward greater environmental sustainability and efficiency.
1. In Terms of Environmental Sustainability
Low-carbon manufacturing technologies will be promoted. Experimental models powered by hydrogen energy have obtained EU CE certification, reducing carbon emissions by 92% compared to traditional equipment, with commercialization expected by 2025.
2. In Terms of Efficiency
The processing capacity and efficiency of the equipment will continue to improve. Through measures such as optimizing blade design, improving motor efficiency, and enhancing control systems, key performance parameters of the plastic shredder, such as shredding ratio and volumetric efficiency, will reach new heights.
As a professional manufacturer of plastic crushers, we are committed to technological innovation and product optimization, providing customers with more efficient, intelligent, and environmentally friendly plastic shredding solutions. We believe that shortly, the plastic crusher machine will play an increasingly important role in the global plastic recycling industry, contributing greater efforts to promoting sustainable development and building a beautiful planet.
Ⅶ. Conclusion
Plastic shredders have evolved from simple mechanical devices to complex equipment capable of integrating artificial intelligence and IoT technology, marking significant technological advancements and application innovations. Today, people do not just use these machines to make plastic smaller. These machines are now a key part of the circular economy system. They help solve global plastic problems. They also help put green development ideas into practice.
The plastic crusher machine will continue to drive the development and transformation of the plastic recycling industry through continuously enhanced levels of intelligence, efficiency, and specialization. Their practical applications demonstrate that technology not only brings convenience but also helps solve environmental issues and brings about positive changes.